Know how and Expertise serving your company
The integrity of the containers operating in the oil and Gas industry is conditioned by the characteristics of the fluids they contain, their date of manufacture/assembly and the preventative maintenance carried out throughout their useful life.
The efficient use of the different phases of a maintenance program (inactivation-cleaning-repair-sandblasting and painting) is vital in order to achieve execution deadlines that allow the equipment concerned to be put into operation again.
At MERO S.A., we have the experience and technology to achieve these objectives.
Cleaning the Inside of Tanks
Remote operation from outside the tank is now possible thanks to MERO S.A.’s incorporation of the state-of-the-art VCR (Vacuum Cleaner Remote) device, which allows access to Confined Spaces (depending on their complexity) without the need for isolation from the rest of the facilities, resulting in reduced equipment downtime. In case of an emergency, it can be immediately put into operation without the need to remove blocking plates.
If it were a confined space with conventional insulation, exposure of individuals to health and safety risks is minimal, as manual removal of waste and efforts for moving hoses and accessories within the tank are avoided.
This tool has become the most reliable when defining the cleaning of a tank since it can have its own lighting, on-board and/or ambient cameras that allow real-time observation of what is happening inside the enclosure. Additionally, it has a front nozzle for injecting pressurized water, which allows for the removal of high-consistency residues and/or cleaning of surfaces.
Stage 2: Envelope Cleaning
Cleaning is carried out by traditional methods, but we also have an Ultra High-Pressure Service of up to 20,000 PSI, which allows reaching inspection cleaning levels by removing encrustations, poorly adhering paints, etc. This is achieved by applying rotating heads that cover a large surface area with high efficiency, reducing execution times.
In addition, we have developed a remote operation system to access high areas without the permanent presence of people on scaffolding, resulting in less exposure to health and safety risks for individuals.
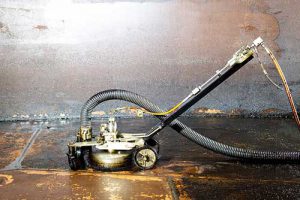
The final result means a cleaning with an inspection level, detecting pittings, cracks, defective welds, etc.
External Tank Cleaning
Stage 4: Robotized Cleaning at Height
Through the combination of devices and our own Process development, we can provide a Safe and Reliable Service for the external cleaning of tanks, applying pneumatic tele-commands that allow the cleaning equipment to be operated from the ground, avoiding work at height for people. This way, pollution is practically eliminated, an inspection level of cleaning is achieved, and execution times are reduced. Many facilities are not intervened due to the difficulties of working at height and the obstacles encountered. With this tool, the path to a Safe and Quality result is simplified.